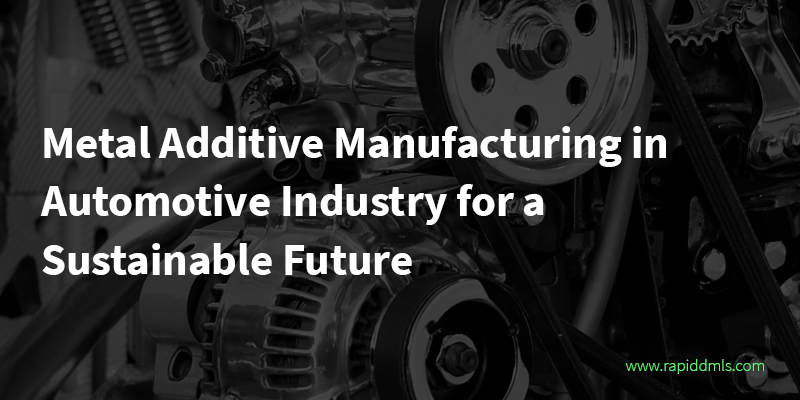
Metal Additive Manufacturing in Automotive Industry for a Sustainable Future
The Automotive Industry as of today has gone through a major revolution since its inception in the late 19th century. The saturation of cars in the entire world has reached 20% i.e., 1.5 billion cars for a population of 7.6 billion people. There is no doubt that owning an automobile, especially a car, has become easier lately. Due to the cut-throat competition in the market, automakers have been manufacturing variants of a car model to cater to all the budget segments.
Although this demand is a good thing for the Automobile Industry, the emission of greenhouse gases is a serious threat to our sustainability in the near future. Around 95% of all the vehicles moving on the roads are equipped with conventional Internal Combustion engines which are powered by petroleum fuels such as petrol and diesel. Petroleum fuels are derived from fossil fuels, which is a non-renewable source of energy.
Burning petroleum fuels in automobiles releases gases such as Carbon di-oxide (CO2), Methane (CH4), Nitrous Oxide(N2O) and other gases from the tailpipe into the atmosphere. These gases trap the incoming solar energy keeping it closer to the earth’s atmosphere, thus increasing the temperature of the Earth’s surface.
Carbon di-oxide alone accounts for three quarters of the emissions bringing its volume in the atmosphere to a whooping 412 ppm (parts per million) compared to 280 ppm at the beginning of the industrial revolution. While the transportation sector contributes to 30% of the total greenhouse gas emissions, generation of electricity using fossil fuels and industry emissions are not far behind.
As important as it is for CO2 to prosper life on Earth, just doubling its concentration in the atmosphere (around 600ppm), would make things uncomfortably hot and cause us some serious problems. Burning fossil fuels also depletes oxygen and lowers the ratio of oxygen to nitrogen in the future.
In order to prevent the above ill effects from happening, vehicles need to be powered by electricity. Electric vehicles need to be stronger and lighter in design which can be realized by incorporating Metal Additive Manufacturing in the Automotive Industry. Automotive companies have already started working towards the realization of electric vehicles. Also, electricity generation needs to be harnessed from renewable sources such as solar energy instead of using fossil fuels.
Carbon Footprint of the Electrified Automotive Industry
Just because electric vehicles are used does not mean that carbon emissions are eliminated completely. Manufacturing of electric vehicles do account to the emissions of CO2 in terms of emissions during electricity generation, emissions from manufacturing the battery, emissions from manufacturing other components of the vehicle.
If solar energy is used to generate electricity instead of fossil fuels, CO2 emissions in terms of electricity generation is nullified which leaves us with carbon emissions from manufacturing battery and other parts of the automobile, which is still 60% lesser emissions compared to the entire lifetime emission of conventional vehicles.
While comparing the emissions of conventional vehicles to electric vehicles, it is important to note that by switching to electric, the initial carbon emissions during manufacturing is compensated in the first couple of years of driving the vehicle with no tailpipe emissions.
Carbon Footprint of Metal 3D Printing (Powder Bed Fusion)
The University of Groningen in the Netherlands found that Metal AM could reduce the overall CO2 emission intensities of industrial manufacturing by up to 5% by 2025. Carbon Footprint during the process of printing depends on the part geometry, in that it is more environmentally sustainable to subtractive manufacture a solid cube, whereas it would be more sustainable to print a lightweight part with lattice structures or hollow channels.
It is also known that 3d printing is more material-efficient than conventional manufacturing, in that it deposits material only at required places by minimizing material wastage compared to a process like machining with lot of scrap. Also, 3d printing just needs STL files for printing which can be transferred digitally. This prevents the emissions that could occur while transportation of parts to multiple locations for conventional manufacturing.
Why Metal 3D Printing has limited applications in IC engine driven Automotive Industry
Automotive components today are designed keeping in mind conventional manufacturing processes. This makes the parts bulky which doesn’t make sense to 3d print the parts. Also, since conventional manufacturing processes handle huge quantities, 3d printing is not a viable option for end use parts.
Metal AM currently finds application in rapid prototyping of new designs to arrive at the best functioning design, using conformal cooled dies for efficient cooling of components manufactured through pressure die casting and injection moulding, and printing of certain obsolete spare parts.
Why Metal 3D Printing has unlimited applications in an electrified Automotive Industry
In order for the automobile industry to be powered by electricity, the automotive parts need to be lighter, stronger and functionality driven. This trend aligns with the trend of Metal 3D Printing. Metal AM will be an efficient process to directly manufacture most of the critical parts that go into an automobile.
For better performance, vehicles have to be stronger, lighter and safer. The individual parts might need to be complex in design to support alternative drive systems. Unlike conventional designs, Metal AM designs can be easily modified depending on the part functionality. This freedom of design is unseen in any other manufacturing process, and will be on the rise with further improvements in technology. Depending on the temperature zone and functionality of a part, multiple alloys ranging from Aluminium to Titanium to other super alloys, can be chosen to arrive at the best strength to weight ratio.
The vehicles of the near future will be autonomous, connected and shared. The vehicles have to be more and more fuel efficient. This means that production quantity of a certain vehicle model has to be restricted to an optimum number as a newer efficient model will have to follow it. This is an ideal setup for Metal AM. Mega printers with multiple lasers and inbuilt post-processing units can instantaneously start serial production of a new part without any down time for setup. This eliminates keeping inventory of the parts as well.
Conclusion
Localized machine manufacturing and localized powder manufacturing should ultimately bring down the cost of manufacturing 3D-printed parts. The cost of automobiles should also come down once Metal Additive Manufacturing in Automotive Industries is considered as an integral manufacturing tool. Although reaching this stage is quite a journey on its own, it is just one of the baby steps towards a sustainable future.