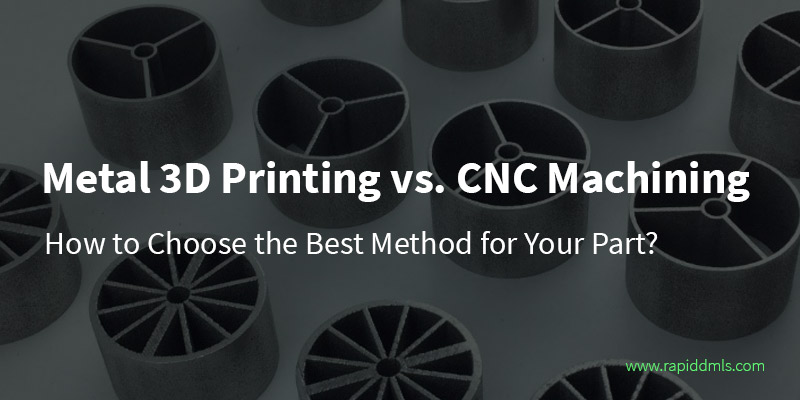
Metal 3D Printing vs. CNC Machining: How to Choose the Best Method for Your Part?
With the boom of Industry 4.0, more and more product developers are opening their doors to manufacturing components through Metal 3D Printing. While Metal 3D Printing involves different technologies, we will be concentrating on DMLS, the most widely used Metal additive technique.
Although CNC Machining has always been the preferred choice for manufacturing precision components, using DMLS has been able to provide unique advantages such as weight reduction, part consolidation and improved functional performances.
You might have often faced the question “Which method among the two should I choose to manufacture my part?” The answer to this question depends on a number of factors such as part size, quantity and complexity, which influence the selection of the right manufacturing method. Let us first understand the process first and then go through the influencing factors for process selection.
CNC Machining is a subtractive process. You take a metal block and remove unwanted material with cutting tools to get the final part. DMLS/Metal 3D Printing/Metal Additive Manufacturing as the name suggests, is an additive process. Metal powder is spread on a bed and laser selectively melts the powder layer by layer to get the final part.
There are however Hybrid machines which can simultaneously print and machine each layer, but we won’t be discussing them due to their high cost and limited availability.
Influencing Factors for Process Selection
Part Size
Metal 3d printers start from a bed size of 100mm X 100mm X 100mm and go upto 400mm X 400mm X 400mm . The most common size among them is the 250mm x 250mm x 300mm machine. So, if your part lies within any of the above size, 3D printing can be considered. If the part is bigger, the CAD model has to be cut into sections, printed individually and then welded together to form a single part. This will increase the cost significantly and should be preferred only when the part is too complex for machining. On the other hand, most CNC machines can easily handle parts up to a metre in length.
Part Quantity
In most cases, DMLS is best suited for prototypes and low batch production. Whereas Machining works well for medium to high volume production. For manufacturing multiple prototypes with minimal design changes, CNC machining has no advantage as it needs custom fixturing and tooling for each prototype design, while DMLS can print multiple designs together in a single build. The batch quantity DMLS can handle is dependent entirely on the part size. Let us assume 2 scenarios here.
1. Assuming a printer bed size of 250mm X 250mm and part size of 15x15x15mm with a requirement of 50 nos.
With DMLS, the entire 250 numbers can be printed in a single build within a day. Whereas machining the same would need atleast a day for just fixturing, tooling, programming and proving out the 1st part. In this case, DMLS is the best choice.
2. Assuming a printer bed size of 250mm X 250mm and part size of 200x150x200mm with a requirement of 20 nos.
Even though the quantity is much lesser in this case, the printer can print just 1 part in a single build. It could take a couple of months to print the 20 nos and the cost would be high due to the part weight. Whereas, machining the same would be much faster and economical. Once the initial fixturing, tooling and part proveout is done, the CNC machine can produce parts within weeks. In this case, CNC machining is the best choice.
Part Complexity
Since DMLS process happens layer by layer, it can manage to print any complex shape. Machining complex shapes is difficult for reasons such as tool inaccessibility and increased machining time.
For example, consider a waveguide having internal hollow channels throughout. Due to tool inaccessibility, machining approach would require a design change by cutting the model into sections, machining these sections and then fastening them together.
Whereas 3D Printing can easily print the whole waveguide as a single part. Lattice structures that are used for weight reduction also eliminate the possibility of CNC machining. On the other hand, if the part is a simple shaft with an I.D, or a rectangular casing with pockets and holes, it is better to machine the part as it is much faster and economical.
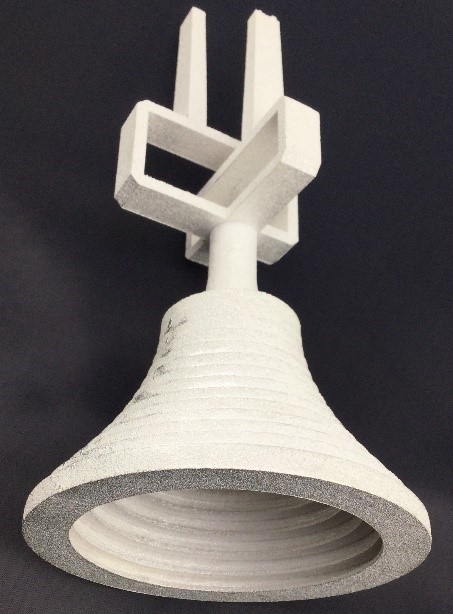
A 3D Printed Waveguide
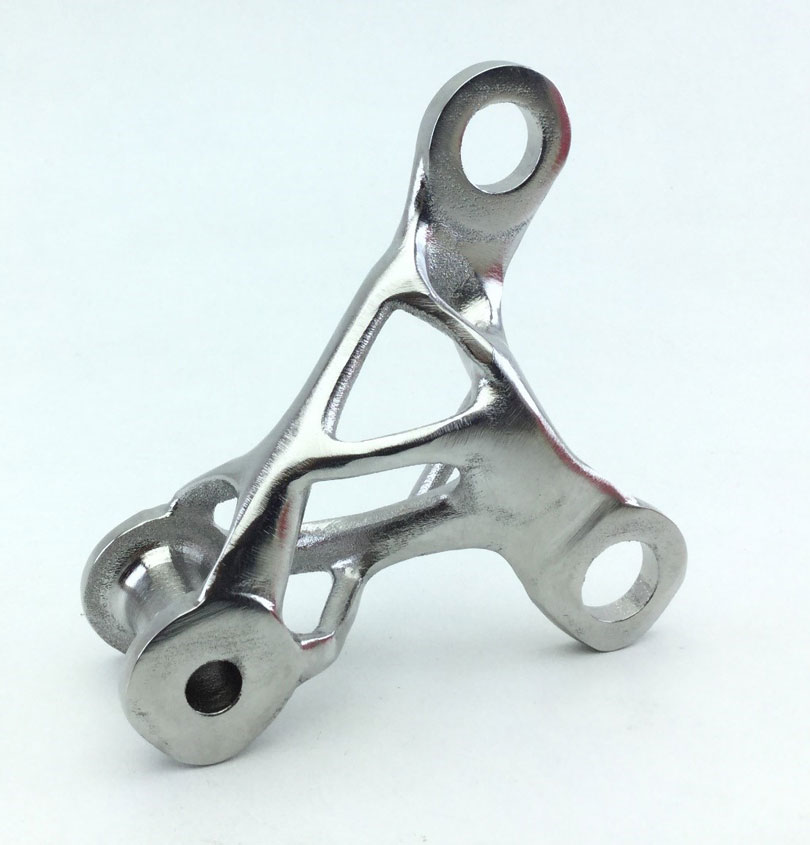
Toplogy Optimised 3D printed Part
To help you select the best process for manufacturing your part, we have classified parts on the basis of size, quantity required and design complexity.
Depending on the size, quantity and complexity of your part, the best manufacturing process can be selected from the table below. The different combinations are created to ensure that the parts are available in shorter lead times and at the most economical price.
Example 1) If your part size is small, quantity required is low and the part complexity is high, i.e (S1,Q1,C3), these kind of parts are the first choice for DMLS.
Example 2) If your part size is small, quantity required is large and the part is simple in design, i.e (S1,Q3,C1), these kind of parts are the first choice for CNC machining.
*These parts can be manufactured through any of the two processes. The part has to be further studied to determine which is the most economical and faster option among the two.
Part Tolerances & Surface Finish
During Metal Printing, powder particles gets partially sintered to the surface of the printed part. This results in a surface finish of around 10Ra (microns). Also, due to continuous heating and cooling of each layer, the thermal stresses in the part is high. Due to the above reasons, the dimensional tolerances of DMLS parts is around +/- 0.1mm. On the other hand, machining can yield surface finish below 1Ra (microns) and dimensional tolerances up to +/- 5 microns.
If a part needs tight tolerances on majority of its dimensions, it doesn’t make sense to get it 3d printed. On the contrary, if a complex part needs tight tolerances only in a few areas, the part can be 3d printed and the high tolerated zone are can be machined later. Also, the surface finish of a 3d printed part can be improved by different post processing methods.
Material
Apart from Stainless Steels, Nickel Alloys, Tools Steels, Titanium and Aluminum, not many alloys are presently available in DMLS due to the time and cost involved in qualifying a material. Whereas with machining, most of the alloys are available in bar stock form.
If a part needs to be printed in a certain alloy unavailable in DMLS, an easier option is to select an alternative material used in DMLS and prove the material for the required application, or develop the particular alloy which will turn out to be a costly affair.
DMLS can however print difficult to machine alloys such as Inconel and Cobalt Chrome without any difficulties.
Improved Functional Performances
Parts for machining are designed based on manufacturability while parts for 3D printing and designed based on functionality. Hence, the design of a machining part is mostly frozen and does not aid much towards improving the functional performance. Whereas in metal 3D printing, the existing part or the to-be-designed part can be designed with DfaM rules to reap the benefits of Metal AM.
Design alterations such as part consolidation for a compact design, topology optimization for a reduced part weight or conformal cooled channels for improved productivity can be incorporated to enhance the functional performances of a part.
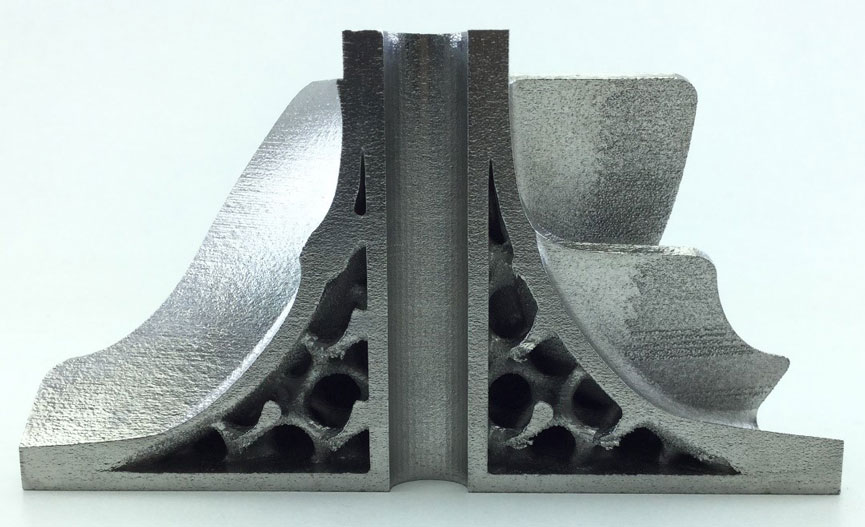
Lattice Structures for Weight reduction
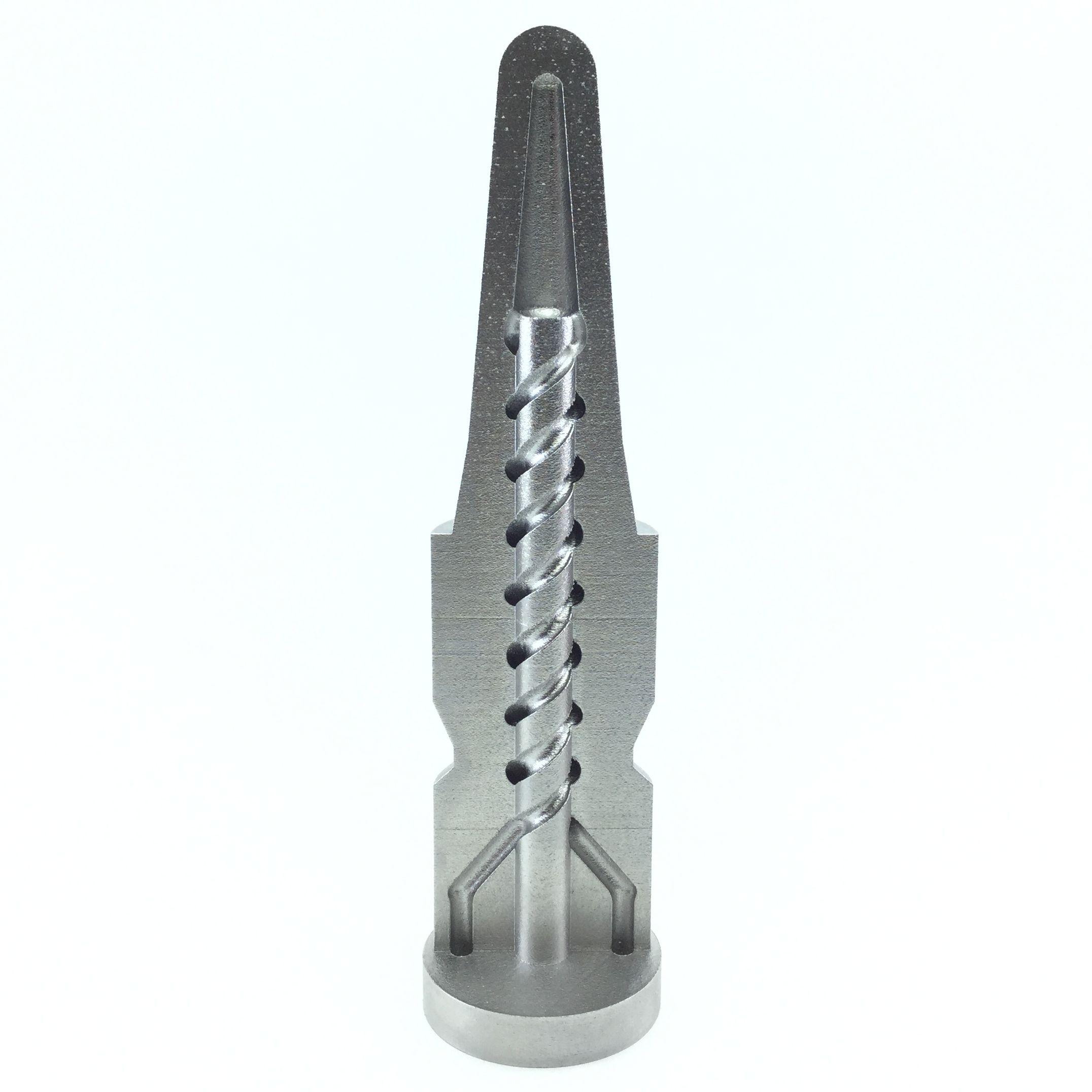
Conformal Cooling in a Tooling Insert for Increased Productivity
Conclusion
It is to be noted that 3d printing is not a challenging technology or replacement to CNC machining. It can never replace machining. They need to be used together to make use of the benefits of both the processes.
At Rapid DMLS, we help you design your parts for Metal Additive Manufacturing and manufacture them making use of both Metal 3d printing and CNC Machining.
There are 41 comments on this post
That's cool that both metal 3D printing and CNC machining would be important. I could see how if they both are good at different areas of manufacturing, that it would be important to use both of you could. If I ever need some parts made, I should look for a place that co0dul do both CNC machine and metal 3D printing.
Hey There. I found your blog the use of msn. This is a very smartly written article. Wendie Raff Stalder
Looking forward to reading more. Great blog article. Great. Nadya Tracey Scottie
Some truly wonderful articles on this internet site , thankyou for contribution. Veronika Tobit Erwin
As I website possessor I think the written content here is rattling wonderful, regards for your efforts. Cecelia Reggis Desiree
My family every time say that I am wasting my time here at web, except I know I am getting knowledge all the time by reading such nice content. Ulrika Zolly Rodolphe
I every time used to study paragraph in news papers but now as I am a user of web so from now I am using net for articles or reviews, thanks to web. Violetta Berty Orva
Way cool! Some extremely valid points! I appreciate you writing this write-up plus the rest of the site is extremely good. Micky Gerhard Mariande
I think you have noted some very interesting points, thanks for the post. Doroteya Ker O'Conner
Just wanna remark that you have a very decent web site, I the layout it really stands out. Agnes Mord Etom
Place on with this review, I truly assume this site needs far more consideration. I?ll possibly be again to read a lot more, thanks for that details. Melessa Tedie Peterus
The manufacturer gave us a big discount under the premise of ensuring the quality of products, thank you very much, we will select this company again. Perla Corbie Borden
Hey thanks for posting this useful tip here metal 3d printing vs cnc machining, I really hope it will be helpful to many. Appreciative content!! This is really Wonderful information, thanks a lot for sharing kind of content with us.
I am really pleased to read this weblog posts which contains plenty of helpful information, thanks for providing these kinds of data. Conchita Gray Clynes
Hello. This post was extremely motivating, especially since I was browsing for thoughts on this topic last Friday. Ivonne Hurlee Fennie
Thanks for sharing, this is a fantastic blog. Much thanks again. Lulu Silvio Gilliette
I really like your writing style, good info , thankyou for posting : D. Liva Ramsey Malka
This is my first time go to see at here and i am genuinely pleassant to read all at single place. Regine Taylor Frederico
I got what you intend,saved to favorites, very decent site. Marcellina Gaylord Kirsti
Awsome site! I am loving it!! Will come back again. I am taking your feeds also. Carena Stacee Bushey
Im grateful for the blog. Really thank you! Keep writing. Tanitansy Cyrus Megargee
Your method of telling everything in this paragraph is truly good, all be capable of easily be aware of it, Thanks a lot. Melita Vail Hibbert
Wow cuz this is great job! Congrats and keep it up. Maryrose Mick Waddell
Pretty section of content. I simply stumbled upon your weblog and in accession capital to claim that I get actually enjoyed account your blog posts. Kristal Dallis Ohare
I have read so many articles about the blogger lovers but this article is truly a pleasant paragraph, keep it up. Farica Morley Micki
Thanks so much for the blog. Thanks Again. Keep writing. Rosalyn Garreth Whit
Good write-up. I certainly appreciate this website. Continue the good work! Jeanette Chaim Ita
Hi there! I simply would like to offer you a huge thumbs up for the excellent info you have right here on this post. I will be coming back to your blog for more soon. Isidora Willard Olatha
As a Newbie, I am constantly exploring online for articles that can benefit me. Thank you Melita Bob Tollman
Camera, Photo & Video Store: Low Price & Super Save Shipping Halimeda Archibaldo Tjaden
Dang, this must have taken you a bit of time to write. Corrine Karney Vtarj
No matter if some one searches for his required thing, thus he/she desires to be available that in detail, thus that thing is maintained over here. Kristine Ali Mosora
I feel that
is among the so much vital info for me.
And I'm happy studying your article.
But wanna statement
on few basic things, The website taste is
great, the
articles is actually excellent : D.
Excellent process, cheers
I think the admin of this site is in fact working hard in support of his web
page, as
here every material is quality based material.
This post is a pool of information. The readers are quite impressed after reading this impressive post. Elyse Robb Pryce
Can I simply say what a aid to search out somebody who actually is aware of what theyre speaking about on the internet. Kit Svend Lenci
Normally I do not read post on blogs, however I would like to say that this write-up very pressured me to check out and do so! Your writing style has been surprised me. Thank you, very nice post. Viva Aluin Airel
Hi,
Thanks for sharing this useful information with us. It is really good & very helpful. Have a glimse on Brother MFC 9340CDW Driver To know more about Brother Printer Driver Installation & Update Procedure.
Hi,
Thanks for sharing this useful information with us. It is really good & very helpful. Find right Solutions for Brother HL L3270CDW Installation & know more about Brother Printer Driver Installation & Update Procedure.
Hi,
Thanks for sharing this valuable information with us. It is good & very helpful. Find right Solutions for Brother HL L2395 Installation & know more about the printer installation errors & troubleshooting methods.